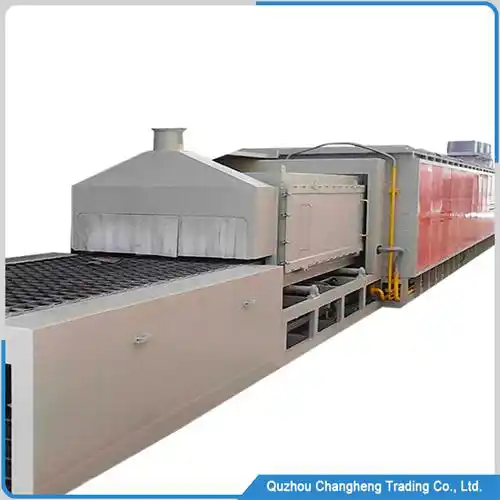
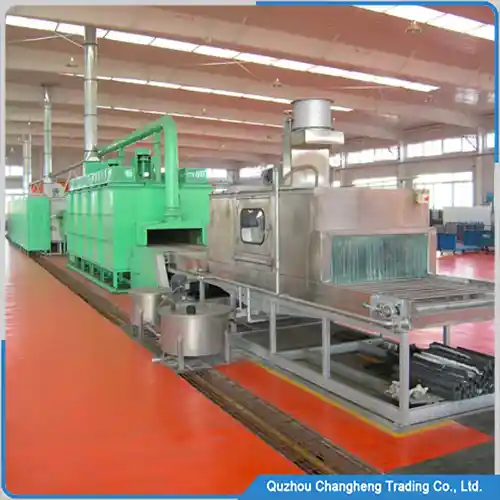
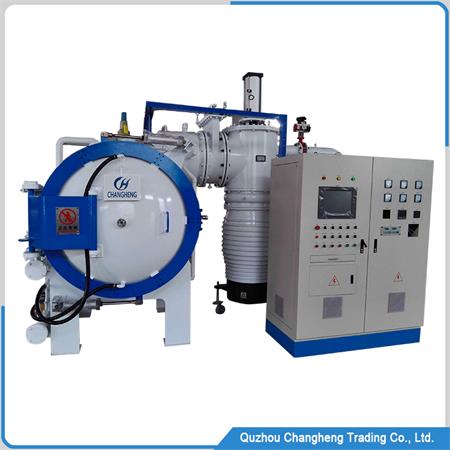
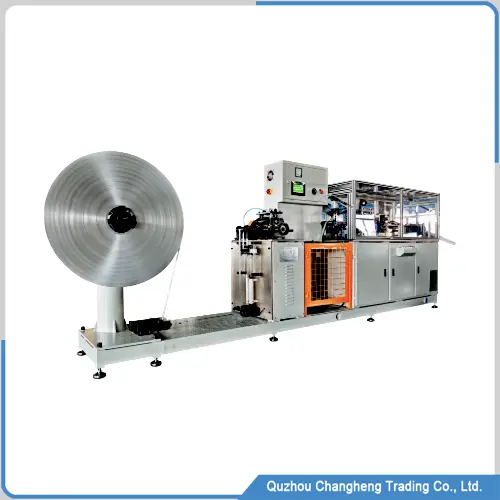
Product Description
This is an aluminum CAB brazing furnace manufactured with the latest technology. The MAFU of the furnace is made of the highest quality SS316L stainless steel material with a thickness of 10mm. The gaps on both sides are welding using argon arc welding technology, which maintains stability during high-temperature use.
The MAFU brazing furnace has a nitrogen delivery pipeline inside, which can protect the product from oxidation during the production process. It is very suitable for large-scale production of aluminum parts, such as aluminum radiators, condensers, intercoolers, and other automotive cooling products,
Scientific structural design
This brazing furnace is composed of multiple devices with different functions, each with a special function to achieve fully automatic continuous production, among which the brazing area is one of the most important devices,
The first layer, from inside to outside of the brazing area, is made of 10mm 316L stainless steel, and the inner side is scientifically arranged with pipes to transport nitrogen gas,
effectively reducing nitrogen consumption and saving usage costs.
The second layer is made of 5mm 304 stainless steel, with advanced heating elements and thermocouples in the middle to achieve precise temperature control.
The two-layer MAFU design of the cab brazing furnace can provide better insulation, and energy will not be wast.
The third layer is asbestos, which protects the heat from going out and achieves uniform internal heat distribution, allowing the factory workshop to have a suitable temperature.
The fourth layer of 2mm carbon steel has 2 layers of high-temperature resistant paint; one layer protects the metal from rusting, and the other layer makes the brazing furnace look beautiful. Users can choose any color.
Compared to our competitors’ CAB brazing furnaces, our equipment has reduced nitrogen usage by 45% and saved 25% on electricity. The same production efficiency reduces operating costs.
Part material of CAB brazing furnace
Part Name | Material |
Conveyor chain | SS304 |
Insulation layer | high-grade asbestos |
MaFu | SS316L |
Frame | ordinary carbon steel |
Thermal insulation curtain | molybdenum |
Outer layer | carbon steel |
CAB Brazing Furnace Technical Parameter
- Maximum temperature: 750 ℃
- Working temperature: 630 ℃
- Workbench height: 90mm
- Drying zone temperature: 300 ℃
- Nitrogen consumption: 120 cubic meters/hour
- Nitrogen purity: 99.999%
- Nitrogen pressure: 6 bar
- Nitrogen pipeline: 50DN
- Production speed: 0-1800mm/min
- Temperature control: Zone 12
- Heating type: electricity and natural gas (optional)
- External dimensions: Customized brazing furnace, dimensions unknown
- Control system: industrial computer
- Touch screen brand: Mitsubishi
- Touch screen size: 17 inches
Advantage of CAB brazing furnace
- Multi-zone temperature control
The brazing furnace is distributed in multiple temperature zones, and each temperature is independently controlled. Local temperature changes will not affect the overall temperature uniformity of the brazing furnace, effectively ensuring smooth output of quality.
- Intelligent control
The control system is the latest, with WIFI data transmission, online updates, intelligent temperature control, data storage, and other functions that can be quickly implement
We also reserve multiple IO interfaces that can link with other devices for control, meeting all the strict requirements of Industry 4.0.
- energy conservation
The innovative structural design significantly reduces the energy consumption of the cab brazing furnace, saving users operating costs.
- Fully automated production
This brazing furnace is in automatic production mode, integrating multiple functions such as degreasing, spraying, brazing agent, drying, brazing, cooling, etc. Workers only need to place the aluminum core on the conveyor chain, and the brazing furnace automatically completes all work.
CAB Brazing furnace usage
This aluminum brazing furnace is widely used in the industrial field. It can adapt to the production needs of different aluminum parts, and it is especially suitable for industries such as automotive, aerospace, electronics, etc.
With the booming development of electric vehicles, there is a high demand for battery cooling plates. More and more factories are investing in producing battery cooling plates, and our CAB brazing furnace is one of the best products for producing battery cooling plates.
Our furnace is your best choice whether aluminum brazing or other heat treatments. With innovative structural design, energy saving, and long-lasting durability, this stove will surely provide value for your factory.
CAB furnace brazing working video
Q & A
A: Yes, this brazing furnace can braze various aluminum material products.
A: Each of our brazing furnaces is customized according to customer requirements, meeting this production speed without any technical issues.
A: We provide brazing furnace installation, brazing technology training, etc. We can also send engineers to work in your factory for a long time.