Vacuum brazing is a technology that uses aluminum materials for welding in a vacuum environment. In a vacuum environment, there is no gas interference during the welding process, which can better control the welding quality and strength.
Compared to traditional fusion welding methods, vacuum aluminum welding can better maintain the structure and properties of the material, thereby improving the quality and stability of the product. Vacuum brazing of aluminum products with complex welding structures and small channels has unique advantages
Vacuum aluminum brazing usually uses automated control for welding, and the brazing process does not require too much human intervention. It can weld various shapes of aluminum components,
such as oil coolers, plate & bar type heat exchangers, automotive aluminum parts, etc. This technology is widely used in fields such as aerospace, automotive manufacturing, and electronics.
ITEM | VALUE |
Application | Aluminum |
Machine size | customized |
Equipment certificate | CE |
Cooling | tap water |
Nitrogen | optional |
Advantages of vacuum brazing
1, In a vacuum environment, the oxide film on the surface of aluminum materials will be removed,
thereby reducing or eliminating the impact of surface oxides on welding, making the welded joint purer.
2, Due to the absence of gas in a vacuum environment, harmful impurities such as oxides will not form during the welding process,
which can better ensure welding quality and improve the strength and hardness of welded joints.
3, in the vacuum environment, the heat dissipation rate during welding is slow,
which can reduce the width and depth of the Heat-affected zone and reduce the deformation and crack tendency of the material.
4, Vacuum brazing can be carried out at lower temperatures, requiring lower heat energy,
and the welding process is relatively mild, which can shorten welding time and improve production efficiency.
5, Vacuum aluminum brazing can be applied to the welding of various materials, including metals, ceramics, etc.,
especially for materials that are difficult to perform traditional welding, such as high-temperature alloys, titanium alloys, etc.
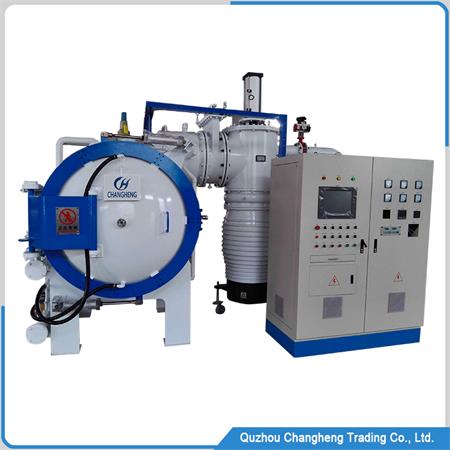
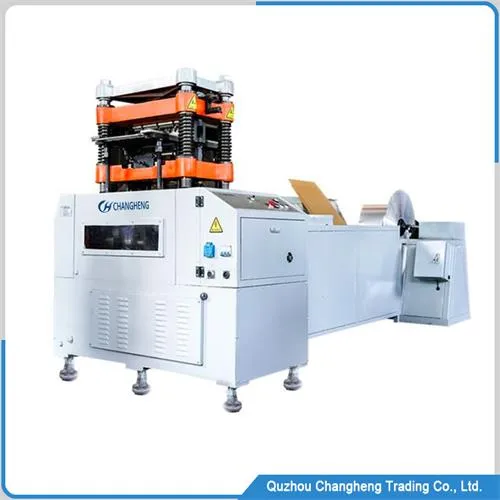
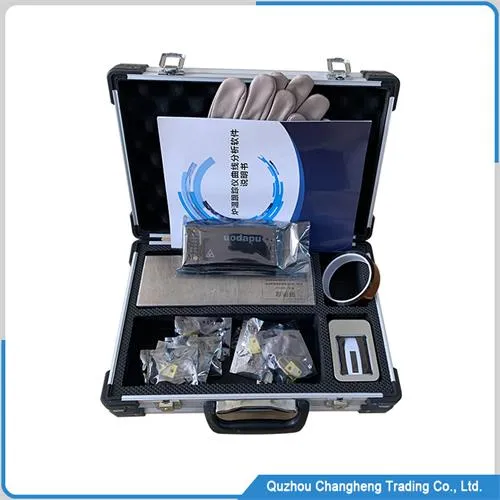
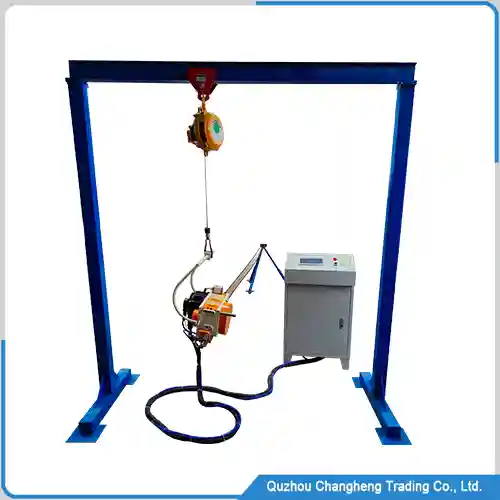
The process of vacuum brazing
Vacuum brazing is a technology that uses welded aluminum material to connect two or more parts together in a vacuum environment.
This welding technology is widely used, and the following are examples of aluminum heat exchanger cores with plate and bar types to illustrate the entire vacuum brazing process:
1, Preparation of parts:
All aluminum parts need to be cleaned using an ultrasonic cleaning machine, and all parts need to be dried Aluminum fins, aluminum plates,
and aluminum bars are placed together according to the design drawings and fixed together using professional tools
2, Place the product:
Place the heat exchanger core that needs to be brazed into the vacuum chamber. Place stably and close the door of the Vacuum furnace
3, Setting control procedure:
the engineer sets each step of the Vacuum furnace, such as vacuuming, temperature heating, cooling water circulation, etc. Each different product can set a separate working step as the operating procedure
4, Vacuum pumping:
Use equipment such as a vacuum pump to extract gas from the vacuum chamber to create a vacuum environment. This helps to reduce the impact of air on the welding process and improve welding quality.
5, Vacuum brazing Heating:
In a vacuum environment, use heating equipment to heat the brazing material above its melting point to melt it. The melted brazing layer then flows into the gaps between the parts, tightly connecting them together.
6, Vacuum brazing Cooling:
after welding, the cooling water begins to circulate, which will cool the Vacuum furnace chamber,
7, Take out the product:
when the temperature drops to 200-260 degrees, the vacuum pump will stop working, the valve on the side of the Vacuum furnace will automatically open, and the vacuum pressure in the chamber will disappear, open the furnace door and take out the aluminum core
Overall, the process of vacuum brazing requires strict quality control and operating procedures to ensure the quality and stability of the welding area.