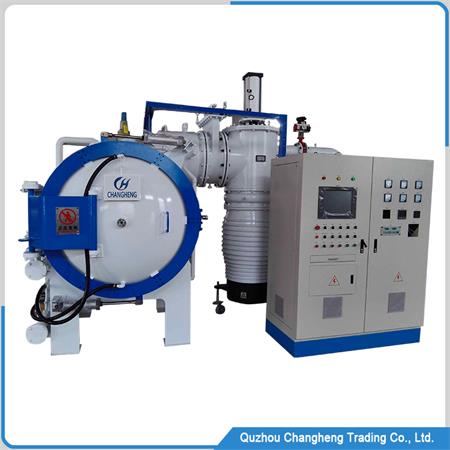
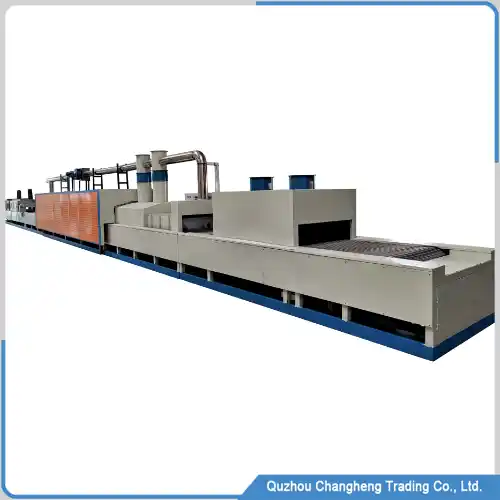
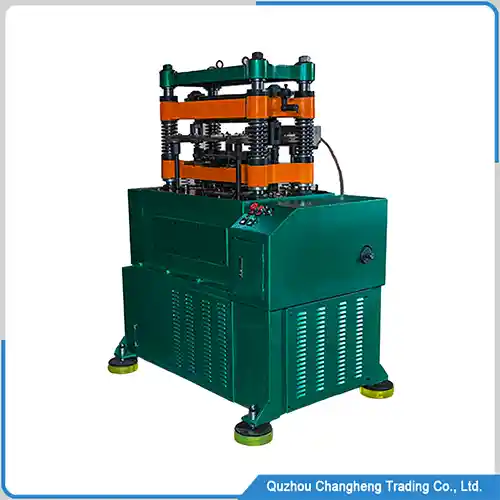

Product Description
The aluminum vacuum brazing furnace is used to braze aluminum alloy materials. It is a device that welds complex parts of multiple aluminum materials in a high-temperature vacuum environment. The entire brazing process does not require any flux.
This equipment usually uses high-temperature vacuum chambers, vacuum valves, vacuum pumps, Roots pumps, transformers, control systems, and other components to form a complete aluminum brazing furnace.
The working principle of a vacuum brazing oven is to place the assembled aluminum heat exchanger core into a high-temperature vacuum chamber and heat the aluminum material in a vacuum environment to reach a high temperature. At this point, the air inside the chamber is extracted, forming a vacuum state.
When the temperature reaches 600+℃, a layer of solder on the surface of the aluminum material melts and mixes. Finally, close the high-temperature vacuum chamber and use a pressure reducer to reduce the indoor pressure to normal. At the same time, the temperature will also decrease, causing the welding material to solidify under normal pressure and form a welded joint.
Vacuum pump system
ITEM | DATA |
DIFFUSER PUMP Liters/sec | 90000 L/s KT -1400 diffusion pump 1 set ZJ -1200 Roots pump 1 set H-150 mechanical pump 1 set |
Valves/cylinders | Stowak |
ROOTS PUMP Liters/sec | 1200 L/s |
Mechanical pump Liters/sec | 150 L/s |
PNEUMATIC SYSTEM Pressure | 0.1Mpa |
PNEUMATIC SYSTEM Pressure | China brand Customized |
Aluminum vacuum brazing furnace Advantages
Good welding quality
braze the aluminum heat exchanger in a vacuum environment, and the aluminum material will not produce an oxide film during welding. The welding points at the welding site are full and firm
Fully automatic control
Workers only need to insert the aluminum heat exchanger into the chamber of the aluminum vacuum furnace and close the furnace door. The equipment will automatically run according to the set brazing program without workers needing to supervise the entire process.
Reduce environmental pollution
The brazing process produces less smoke and dust, and the gas extracted by the vacuum pump passes through an air filter and is discharged into the atmosphere without any pollution.
Dedicated forklift
This vacuum aluminum brazing furnace is already equipped with a dedicated forklift, which allows workers to quickly load and remove the aluminum heat exchanger into the furnace.
Widely applicable
It is suitable for welding various aluminum and its alloy materials and for industries such as aerospace, automotive manufacturing, electronic components, etc.
Good insulation
A cooling water circulation device is in the middle of the entire vacuum aluminum brazing furnace body. During high-temperature brazing, the surface temperature of the furnace body will not exceed room temperature, providing a good experience for the entire working environment
Technical Parameter
ITEM | DATA |
Max Weight | 800KG |
Loading/ Unloading | 90*80*80CM |
Heating element | Nickel-Chromium |
Loading / Unloading | Horizontal loading |
Operating Temp | 575-650℃ |
Temp UNIFORMITY | ±3℃ |
Heating Speed | 300℃ / h |
Touch screen | 15 inch |
Aluminum vacuum brazing furnace video
Q & A
A: Yes, we have configured a 15-inch touchscreen for this machine.
A: I accept any size of vacuum furnace working size, Each machine is customized according to customer requirements.
A: Purchase a vacuum furnace from us and we provide all brazing technical support.