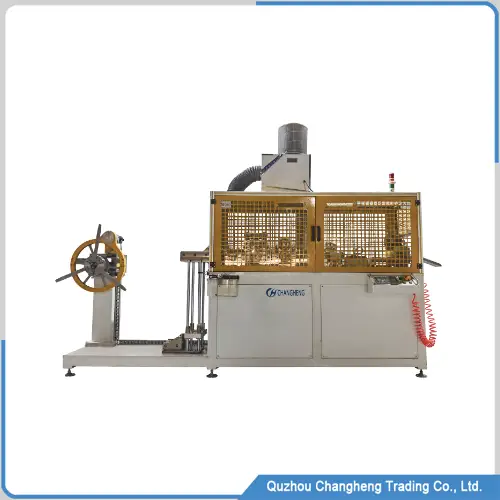
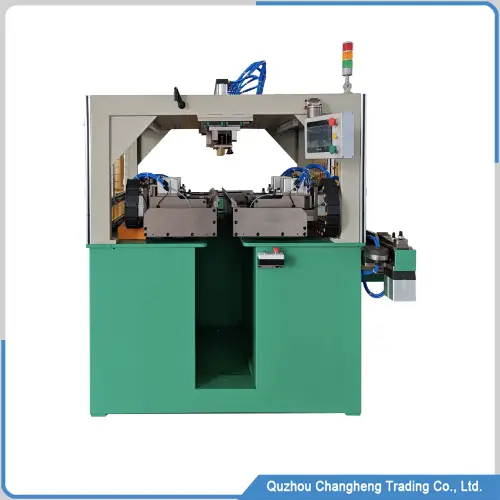
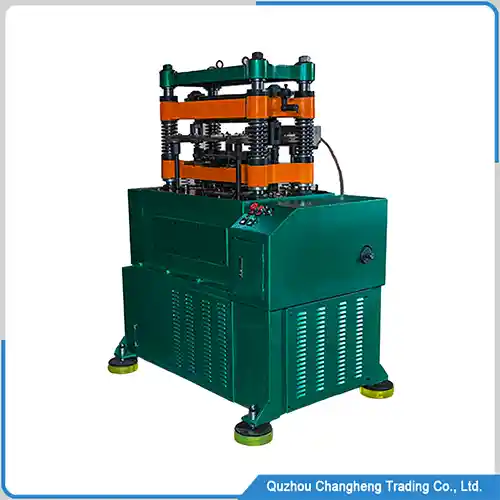
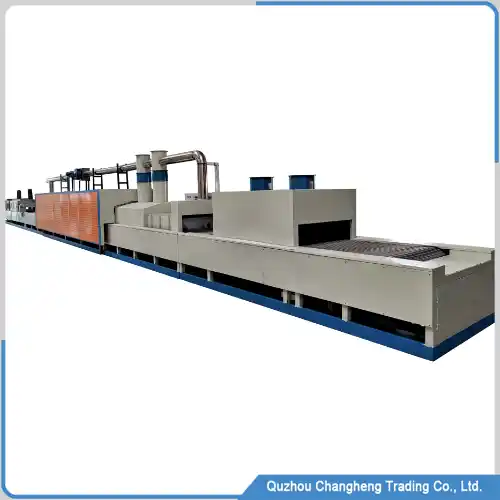
Machine description
This is a radiator fin machine produced by high-speed roll pressing. It has a 2.2kw motor that drives the rollers using a belt. The maximum production speed can reach 120 meters per minute. It is currently one of the most efficient fin production equipment in the radiator and condenser industry.
The machine rotates the number of statistical waves through a servo motor, thereby accurately controlling the length of the fin, ensuring that the length error of each aluminum fin does not exceed 0.1mm. Moreover, the appearance parts of this fin production machine are all made of nickel-plated process, and the surface of the parts shines with a silver light. Even if the machine is used in harsh environments for a long time, these parts will not rust.
The control system is equipped with the latest generation of Mitsubishi brand PLCs, and the sensors also come from internationally renowned brands. The entire control system integrates functions such as real-time monitoring, fault alarm, and preset production capacity, truly realizing the intelligent control of Industry 4.0.
The technical parameters of the radiator fin machine
- Wave height: 4-12mm
- Fin width: 12-160mm
- Pitch range: 2-4mm
- Material thickness: 0.05-0.15mm
- Shape: U-shaped, rectangular
- Material: Aluminum or copper
- Blade material: M36
- Blade hardness: 235~369HBw
- Maximum speed: 120 meters/minute
- Normal speed: 100 meters/minute
- Cutting frequency: Max 60 times/minute
- Inner diameter of the coil material: φ150-300mm
- Outer diameter of the roll: ≤φ1500mm
- Installation dimensions: 5800×1200×1650mm
- Motor power: 3.5kW
- Speed setting: Infinitely variable speed
- Air pressure: 0.4 MPa
- Machine weight: 2.0 tons
Radiator fin machine advantage
This is the latest condenser and radiator fin manufacturing machine, boasting several distinct advantages over other types of fin equipment. Here are some examples of the benefits of this machine.
- Adjust the production speed digitally
The PLC controls the current to the driver, regulating the motor’s running speed. The motor uses a synchronous belt to drive the mold roller of the machine. Engineers can control the production speed of the machine by inputting numbers through the touch screen. This control method achieves accuracy to the millisecond level, providing a truly visual representation of production speed.
- Compact design
This radiator fin machine integrates multiple different functional parts, enabling automated production. It features a compact design, allowing it to occupy minimal space even in large radiator factories or small-scale operations.
- Efficient production speed
The maximum production speed of this machine is 120 meters per minute, which usually requires two workers to sort out the fins. We also have another fin machine, which has an incredible maximum production speed of 300 meters per minute. If your factory requires faster machines, please don’t hesitate to contact us.
- High-precision manufacturing
The parts of this fin forming machine are all manufactured using high-precision technology. Among them, the blade of the fin roller mold is a key part, which is cut and formed using a dedicated machine, and then polished using micron-level equipment to ensure the blade is sharp and the shape of the cut blinds is without burrs.
Radiator fin machine working video
The advanced features of the Fin machine.
Intelligent lubrication device.
When the radiator fin machine is running at high speed, the roller molds and aluminum foil rolling will generate a lot of heat. Spraying volatile oil can not only lubricate the roller molds but also play a cooling role. This machine is equipped with a volatile oil lubrication device, which automatically sprays oil indirectly. Excess lubricating oil can be recycled to the oil tank for reuse.
The fuel tank is equipped with a liquid level sensor. When the volatile oil level is below the set value, the machine emits an alarm signal, prompting workers to add lubricating oil to prevent mechanical failure due to a lack of volatile oil during regular operation. This design not only enables the equipment to produce stably and reliably over a long period but also extends the machine’s lifespan.
Automatic adjustment of material tension.
The hardness of materials produced by different factories may vary, and so does the hardness of copper and aluminum materials. Therefore, this machine is designed with a device for automatically adjusting tension, which ensures adaptability to different materials and varying hardness levels.
When you change the raw materials from different factories, you don’t need to modify any production parameters or adjust any tools for this machine. The fin machine automatically adapts to these materials.
Modular mold design.
The radiator industry offers a wide range of sizes, resulting in various fin shapes and sizes. To meet the diversified production needs, our radiator fin machine molds adopt a modular design. Users can replace the roller molds with different radiator fins to produce various fins, meeting the needs of customers.
Since this mold is an entirely independent entity, replacing it is a very convenient process. Even an ordinary worker can replace it in less than an hour.
Other more radiator machines
Manual crimping machine of car and truck radiators
Machine Overview The manual crimping machine mainly produces car and truck radiators. Some people say it is a semi-automatic crimping machine. A cylinder drives its pressing arm and is installed on a linear slide rail. The mechanical arm moves smoothly…
Core assembly machine of radiator | intercooler core builder
Purpose of equipment The fully automatic core assembly machine is one of the production equipment for engines and radiators. Multiple servo motors mainly drive it, and the aluminum tube automatically drips. Workers only need to install the fin, and the…
Radiator testing machine of High-precision
Product Description This radiator testing machine is used to check the air tightness of various types of automotive radiator products Compared to the previous generation of machines, this instrument has enhanced the expansion of output ports, quality management, and communication…
Radiator clinching machine of cars and trucks
Machine Overview This radiator clinching machine is mainly used to produce radiators. Radiator core, sealing gasket, and plastic tank; put them together The machine combines a servo motor drive and a cylinder drive. The electric control system adopts PLC, touch…
High-quality materials.
The core material of this machine is the blade of the roller mold. We not only need to consider its hardness and wear resistance, but also take into account its strength and toughness, to ensure the machine’s service life and the stability of the fin quality.
The material of our radiator fin machine’s roller mold blade is M36 (the American equivalent is T11336). This material can still maintain a high hardness in a high-temperature environment of 600°. After high-temperature vacuum quenching and tempering, its hardness can be kept at 60-69HRC.
This metal material contains elements such as cobalt, tungsten, molybdenum, and vanadium. By strengthening its properties according to scientific principles, we can enhance its wear resistance and toughness, ensuring the material meets the high standards of tool-grade quality.
If the material is aluminum, then this roller mold can be used for 8 hours a day, and its lifespan can be as long as 10 years.
Let’s summarize in the end.
This radiator fin machine is made of high-strength metal materials and features an intelligent control and lubrication system, enabling an exceptionally long service life for the machine. It not only achieves precise cutting technology, but also runs at a high speed of 120 meters per minute smoothly. It is an indispensable equipment in radiator factories at present.
If you’re looking for a fin-making machine to meet your production needs for radiators or condensers, then this device might be one of your best choices. You can fill out the form below, and our engineers will contact you to provide more details about this machine.